“Properties of SD POLYCA™”
- Fabrication processing condition
- Physical properties
- Moisture absorption curve
- Drying Curve
- Spiral flow
- Temperature dependence of refractive index
- Wave length dependence of light transmittance
- Long term weatherability
- Influential factors on impact strength
- Heat aging property
- Stress concentration and fatigue property
- Temperature dependence of flexural modulus
- Chemical properties/Chemical resistance of SD POLYCA™
- UL Standards
- Material registration in compliance with PSE law
To ask more questions on our products,please refer here
Fabrication processing condition
Grade | Drying Condition |
Standard Processing Temperature (°C) |
Mold Temperature (°C) |
---|---|---|---|
301-4 | 125°C、 4~6Hr | 315-340 | 70-100 |
301-6 | 125°C、 4~6Hr | 300-325 | 70-100 |
301-10 | 125°C、 4~6Hr | 290-315 | 70-100 |
301-15 | 125°C、 4~6Hr | 280-300 | 70-100 |
301-22 | 125°C、 4~6Hr | 265-280 | 70-100 |
301-30 | 125°C、 4~6Hr | 250-260 | 70-100 |
301-40 | 125°C、 4~6Hr | 250-260 | 70-100 |
SD2201W | 120°C、 4~6Hr | 280-300 | 70-100 |
775-20 | 125°C、 4~6Hr | 270-290 | 70-100 |
776-20 | 125°C、 4~6Hr | 270-290 | 70-100 |
875-20 | 125°C、 4~6Hr | 270-290 | 70-100 |
876-20 | 125°C、 4~6Hr | 270-290 | 70-100 |
877-20 | 125°C、 4~6Hr | 270-290 | 70-100 |
878-20 | 125°C、 4~6Hr | 270-290 | 70-100 |
875G10 | 125°C、 4~6Hr | 280-300 | 80-110 |
875G20 | 125°C、 4~6Hr | 280-300 | 80-110 |
875G20F | 125°C、 4~6Hr | 280-300 | 80-110 |
SI 6001W | 115°C、 4~6Hr | 265-280 | 70-100 |
LR 8031V | 125°C、 4~6Hr | 265-280 | 70-100 |
LR 8061V-F10 | 125°C、 4~6Hr | 265-280 | 80-110 |
LR 8081W | 125°C、 4~6Hr | 265-280 | 70-90 |
ST 5101V | 125°C、 4~6Hr | 280-300 | 80-110 |
ST 5201V | 125°C、 4~6Hr | 280-300 | 80-110 |
ST 5301V | 125°C、 4~6Hr | 280-300 | 80-110 |
ST 5031V-G10 | 125°C、 4~6Hr | 280-300 | 80-110 |
IM 5101V | 120°C、 4~6Hr | 280-300 | 80-110 |
CF 5101V | 125°C、 4~6Hr | 280-300 | 80-110 |
CF 5201V | 125°C、 4~6Hr | 280-300 | 80-110 |
CF 5301V | 125°C、 4~6Hr | 280-300 | 80-110 |
CS 5005 | 125°C、 4~6Hr | 265-280 | 70-100 |
CS 5010 | 125°C、 4~6Hr | 265-280 | 70-100 |
CS 5015 | 125°C、 4~6Hr | 265-280 | 70-100 |
IM-401-10 | 120°C、 4~6Hr | 280-300 | 70-100 |
IM-401-18 | 120°C、 4~6Hr | 260-280 | 70-100 |
IM-401-28 | 120°C、 4~6Hr | 250-260 | 70-100 |
IM 6110 | 110°C、 4~6Hr | 250-270 | 50-80 |
IM 6011 | 100°C、 4~6Hr | 240-260 | 50-80 |
IM 6120 | 115°C、 4~6Hr | 260-280 | 50-80 |
IM 6023 | 100°C、 4~6Hr | 240-260 | 50-80 |
PCX-3655 | 115°C、 4~6Hr | 270-290 | 60-80 |
PCX-10325B | 120°C、 4~6Hr | 260-280 | 70-110 |
CR 3241 | 120°C、 4~6Hr | 270-290 | 70-100 |
CR 3241-10G | 120°C、 4~6Hr | 280-300 | 80-110 |
CR 3441 | 115°C、 4~6Hr | 260-280 | 70-100 |
CR 3441-10G | 115°C、 4~6Hr | 260-280 | 80-110 |
CR 3420T | 120°C、 4~6Hr | 260-280 | 70-100 |
CR 3341T | 120°C、 4~6Hr | 260-280 | 70-100 |
Moisture absorption curve
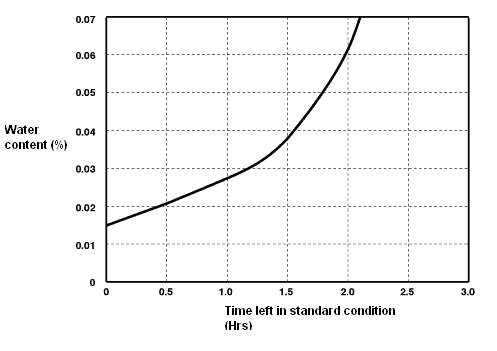
Drying Curve
Forced convection oven dryer
Initial water content: 0.18%
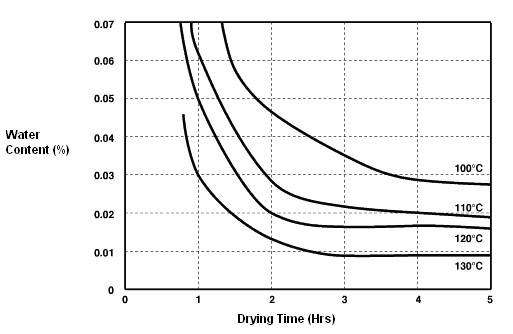
Spiral flow
SD POLYCA™
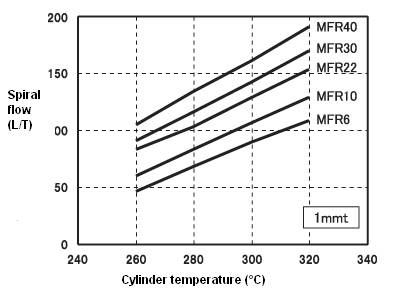
Injection machine/ JSW J100SAII
Mold / 10mm x 1mmt Spiral mold
Molding condition /
Injection pressure: 157MPa (1600Kg/cm^2)
Injection speed: 50%
Mold temperature: 80°C
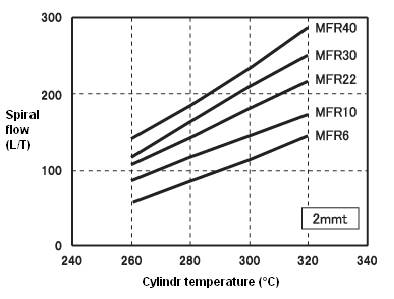
Injection machine/ JSW J100SAII
Mold / 10mm x 2mmt Spiral mold
Molding condition
Injection pressure: 157MPa (1600Kg/cm^2)
Injection speed: 50%
Mold temperature: 80°C
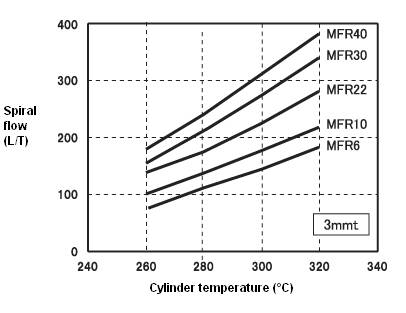
Injection machine/ JSW J100SAII
Mold / 10mm x 3mmt Spiral mold
Molding condition
Injection pressure: 157MPa (1600Kg/cm^2)
Injection speed: 50%
Mold temperature: 80°C
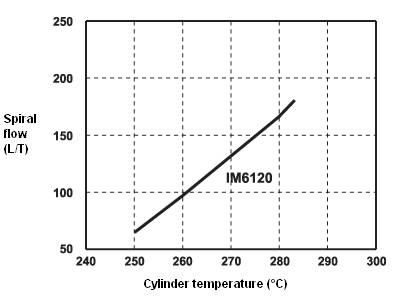
Injection machine / Toshiba Machine IS-90B
Mold / 10mm x 3mmt Spiral mold
Molding condition /
Injection pressure: 78MPa (800Kg/cm^2)
Injection speed: 20%
Mold temperature: 50°C
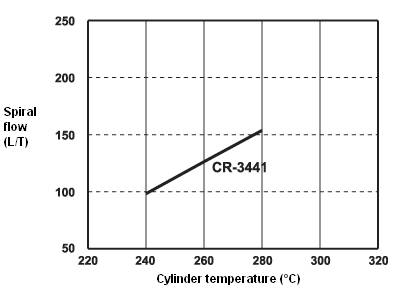
Injection machine / Toshiba MachineIS-100FIII
Mold / 10mm x 3mmt Spiral mold
Molding condition /
Injection pressure: 98MPa (1000Kg/cm^2)
Injection speed: 50%
Mold temperature: 60°C
Temperature dependence of refractive index
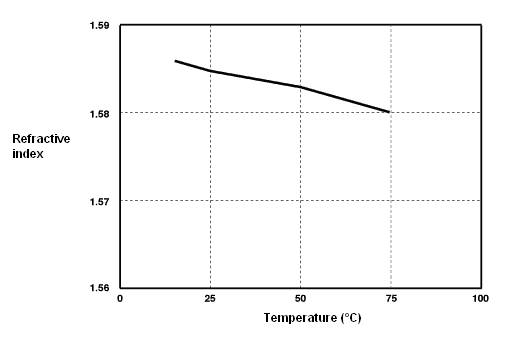
Wave length dependence of light transmittance
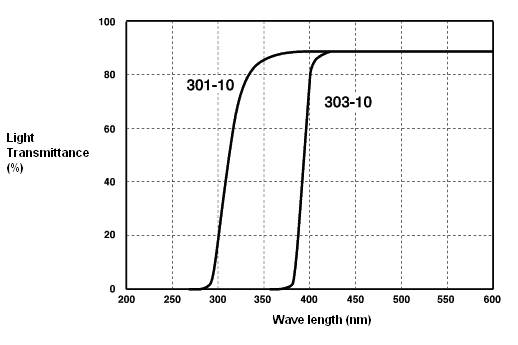
Long term weatherability
Transmittance
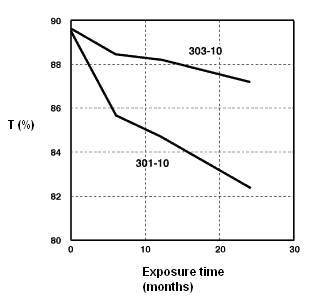
Delta YI
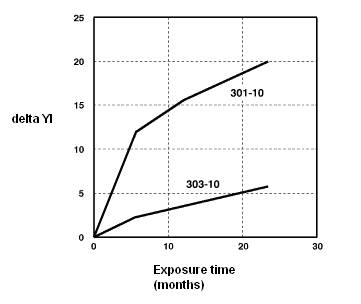
Haze
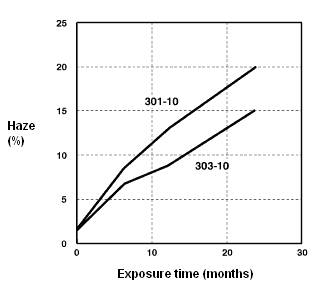
Impact strength (23 degC)
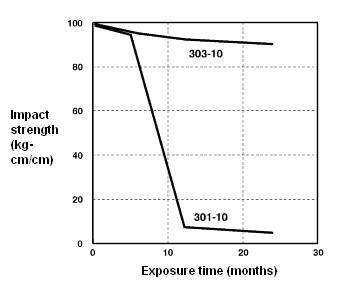
Delta YI
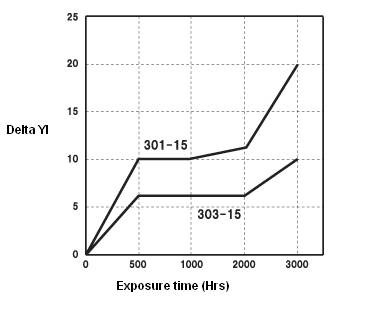
Delta YI
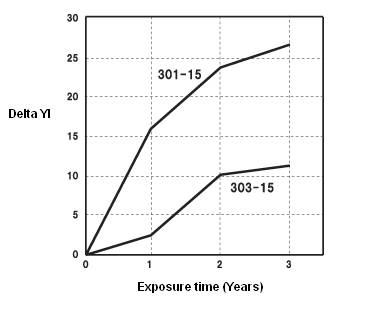
Influential factors on impact strength
Notch Radius
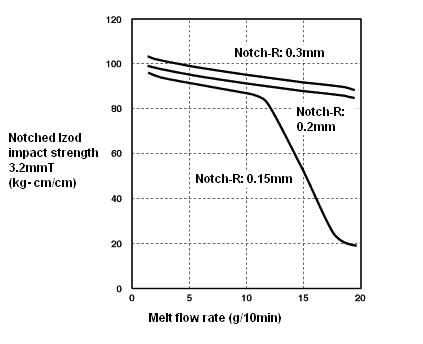
Temperature
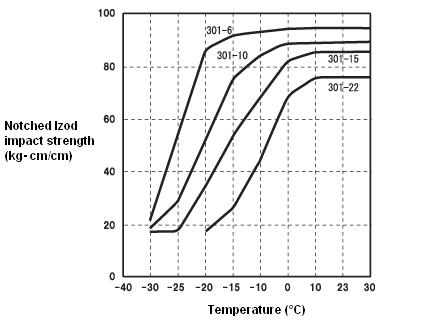
Heat aging property
Yellowing index
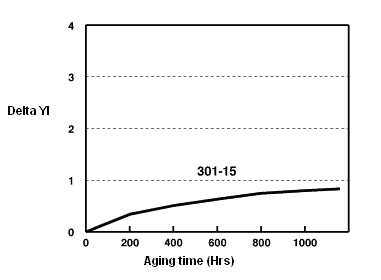
Molecular weight change
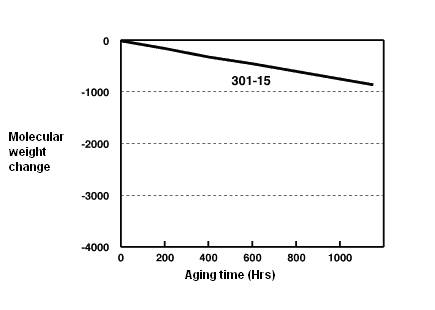
Stress concentration and fatigue property
Stress concentration at corner
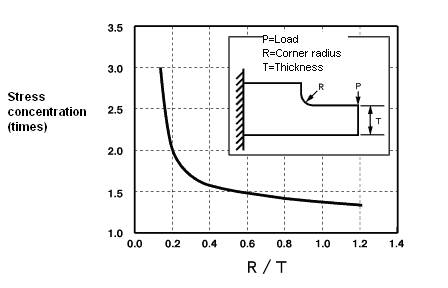
Fatigue property
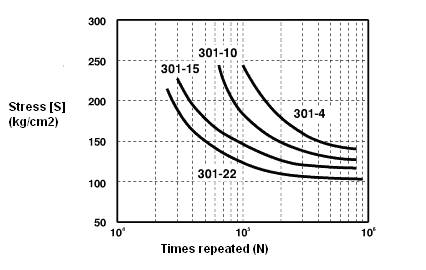
Temperature dependence of flexural modulus
SD POLYCA™
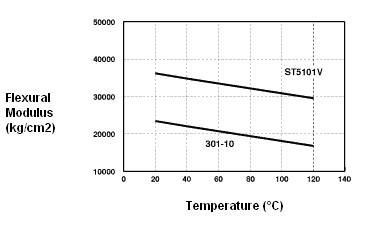
PC/ABS Alloy
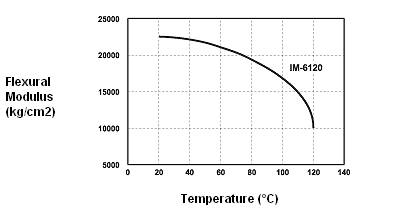
PC/PBT Alloy
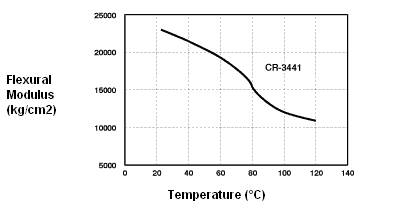
Chemical properties/Chemical resistance of SD POLYCA™
Level of chemical attack (Appearance change)
Chemical | PC | PC/PET | PC/PBT |
---|---|---|---|
Sulfuric acid | A | A | A |
Sodium hydroxide | A | A | A |
Ethyl alcohol | A | A | A |
Acetone | C | B-C | B-C |
Carbon tetrachloride | B | B | B |
Saline water | A | A | A |
Gasoline | A | A | A |
Kerosene | A | A | A |
Wax remover | A | A | A |
Engine oil | A | A | A |
Machine oil | A | A | A |
Grease | A | A | A |
Air refreshener (for auto.) | C | A | A |
Brake fluid | C | B | B |
Salad oil | B | B | B |
Toluene | C | B | B |
Acetic acid | B | B | B |
Judgment:
A: No visual change after dipping for 5 min
B: Slight change after dipping for 5 min
C: Cause whitening or dissolution after dipping for 5 min
Critical strain
Chemical | PC | PC/PET | PC/PBT |
---|---|---|---|
Brake fluid(DOT-4) | 0.3 | 0.6 | 0.8 |
Air refreshener (for auto.) | 0.4 | 0.6 | 0.8 |
Armour oil | >1.0 | >1.0 | 1.0 |
Leather wax | >1.0 | >1.0 | >1.0 |
Plasticizer(DOP) | 0.6 | >1.0 | >1.0 |
Gasoline | 0.2 | 0.4 | 0.6 |
Judgment:
- Critical strain is more than 0.7% (Critical stress is more than 160Kg/cm2). It is considered to be safe for use in general.
- Critical strain is 0.5~0.7% (Critical stress is 110~160kg/c㎡). It needs to be confirmed the condition applied.
- Critical strain is less than 0.5% (Critical stress is less than 110kg/c㎡). It is not recommended to use.
Testing Method
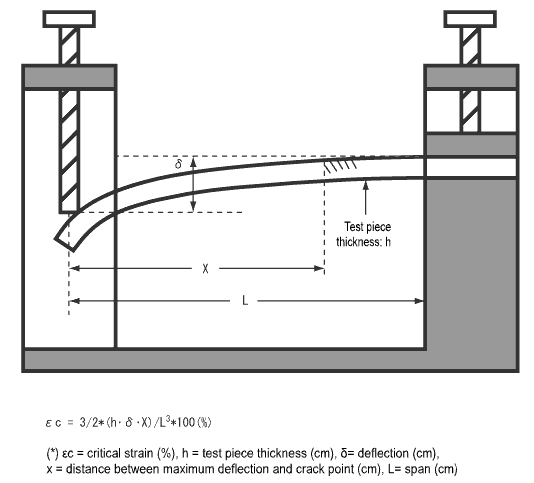
UL Standards
The following our grades are certified by Underwriters Laboratories Inc. and registered in File No. E123529.
Grade | MFR | Color | Thickness (mm) |
Flame Class |
HWI | HAI | R T I | HVTR | D495 | CTI | |||
---|---|---|---|---|---|---|---|---|---|---|---|---|---|
Elec | Mech | ||||||||||||
Imp | Str | ||||||||||||
Polycarbonate resin | |||||||||||||
300, 301 | 3~19 | ALL | 1.5 | HB | 2 | 1 | 125 | 115 | 125 | - | - | - | |
3.0 | HB | 1 | 1 | 125 | 115 | 125 | - | - | - | ||||
302, 303 | 3~19 | ALL | 1.5 | HB | 2 | 0 | 120 | 105 | 120 | - | - | - | |
3.0 | HB | 2 | 0 | 120 | 110 | 120 | - | - | - | ||||
IM-401-10 | 10 | ALL | 1.5 | HB | - | - | 80 | 80 | 80 | - | - | - | |
300, 301 | 3~19 | ALL | 0.44~0.75 | V-2 | - | - | 80 | 80 | 80 | 2 | 5 | 2 | |
20~21 | 0.44 | V-2 | - | - | 80 | 80 | 80 | - | - | - | |||
22~30 | 0.44 | V-2 | - | - | 80 | 80 | 80 | - | - | - | |||
3.0 | V-2 | - | - | 80 | 80 | 80 | - | - | - | ||||
40 | 0.45~0.58 | V-2 | - | - | 80 | 80 | 80 | - | - | - | |||
302,303 | 3~19 | ALL | 0.44 | V-2 | - | - | 80 | 80 | 80 | 2 | 5 | 3 | |
20~21 | 0.44 | V-2 | - | - | 80 | 80 | 80 | - | - | - | |||
22~30 | 0.44 | V-2 | - | - | 80 | 80 | 80 | - | - | - | |||
3.0 | V-2 | - | - | 80 | 80 | 80 | - | - | - | ||||
300V, 301V | 3~19 | ALL | 0.44 | V-2 | - | - | 80 | 80 | 80 | 2 | 5 | 2 | |
0.75 | V-2 | - | - | 80 | 80 | 80 | - | - | - | ||||
1.5 | V-2 | 2 | 0 | 125 | 115 | 125 | - | - | - | ||||
3.0 | V-2 | 1 | 1 | 125 | 115 | 125 | - | - | - | ||||
302V, 303V | 3~19 | ALL | 0.44 | V-2 | - | - | 80 | 80 | 80 | 2 | 5 | 3 | |
1.5 | V-2 | 2 | 0 | 120 | 105 | 120 | - | - | - | ||||
3.0 | V-2 | 2 | 0 | 120 | 110 | 120 | - | - | - | ||||
1080DVD | 80 | NC | 0.38 | V-2 | - | - | 80 | 80 | 80 | - | - | - | |
775-20 | 20 | ALL | 1.5 | V-0 | - | - | 80 | 80 | 80 | - | - | - | |
776-20 | 20 | ALL | 0.75 | V-2 | - | - | 80 | 80 | 80 | - | - | - | |
2.95 | V-0 | - | - | 80 | 80 | 80 | - | - | - | ||||
875-20 | 20 | ALL | 0.95 | V-0 | 2 | 0 | 80 | 80 | 80 | - | 7 | 3 | |
1.5 | V-0 | 2 | 0 | 125 | 125 | 125 | - | - | - | ||||
2.5 | V-0/5VB | 2 | 0 | 125 | 125 | 125 | - | - | - | ||||
3.0 | V-0/5VB | 2 | 0 | 125 | 125 | 125 | - | - | - | ||||
876-20 | 20 | ALL | 1.5 | V-0 | 3 | 0 | 125 | 125 | 125 | - | 7 | 3 | |
2.5 | V-0/5VB | 3 | 0 | 125 | 125 | 125 | - | - | - | ||||
3.0 | V-0/5VB | 2 | 0 | 125 | 125 | 125 | - | - | - | ||||
RP876-20 | 20 | ALL | 1.5 | V-0 | - | - | 80 | 80 | 80 | - | - | - | |
2.5 | V-0/5VB | - | - | 80 | 80 | 80 | - | - | - | ||||
877-20 | 20 | ALL | 1.5 | V-0 | - | - | 80 | 80 | 80 | - | - | - | |
2.0 | V-0/5VB | - | - | 80 | 80 | 80 | - | - | - | ||||
3.0 | V-0/5VB | - | - | 80 | 80 | 80 | - | - | - | ||||
LR8001V | WT | 0.44 | V-0 | - | - | 80 | 80 | 80 | - | - | - | ||
LR8021 | WT | 0.5 | V-2 | - | - | 80 | 80 | 80 | - | - | - | ||
3.0 | V-1 | - | - | 80 | 80 | 80 | - | - | - | ||||
LR8031V | WT | 1.0 | V-0 | - | - | 80 | 80 | 80 | - | - | - | ||
1.5 | V-0 | - | - | 80 | 80 | 80 | - | - | - | ||||
ST5(y)(x)(z) | ALL | 1.5 | V-2 | - | - | 80 | 80 | 80 | - | - | - | ||
3.0 | V-1 | - | - | 80 | 80 | 80 | - | - | - | ||||
IM-401-18 | 18 | ALL | 1.35 | V-2 | - | - | 80 | 80 | 80 | - | - | - | |
3.0 | V-2 | - | - | 80 | 80 | 80 | - | - | - | ||||
Polycarbonate/ABS alloy (PC/ABS) | |||||||||||||
PCX-3655 | ALL | 1.5 | V-0 | - | - | 80 | 80 | 80 | - | - | - | ||
2.0 | V-0/5VB | - | - | 80 | 80 | 80 | - | - | - | ||||
3.0 | V-0/5VB | - | - | 80 | 80 | 80 | - | - | - | ||||
IM6011 IM6110 IM6120 |
ALL | 1.5 | HB | - | - | 60 | 60 | 60 | - | - | - |
ALL: All colors, NC: Natural color, WT: White
(x)0: No additives, 1: Mold release, 2: UV stabilizer
(y)Glass fiber content (10-50%)
(z)V, H, M, L: Melt flow index (V: High ? L: Low)
Material registration in compliance with PSE law
Ball Pressure Temperature
Registration No |
BPT(°C) | Grade | MFR |
---|---|---|---|
B-1975 | 130 | 300~303 350~353 |
10, 15, 22, 30 |
B-1979 | 135 | 300~303 350~353 |
4, 5, 6, 8 |
B-2075 | 135 | ST5100~ST5503 | L, M, H, V |
B-2080 | 135 | CF5100~CF5503 | L, M, H, V |
B-2744 | 135 | 875-20 | 20 |
Horizontal Burn Test
Registration No |
Burningrate (mm/min) |
Thickness (mm) |
Grade (All color) |
MFR |
---|---|---|---|---|
H-1083 | 40 | 0.8 | 300~303 350~353 |
4~22 |
H-0429 | 40 | 0.9 | ST5050~ST5503 | L, M, H, V |
H-1845 | 40 | 1.5 | 875-20 | 20 |
Drying of Polycarbonate before processing is necessary because of its water absorbing behavior. Under normal conditions, Polycarbonate will absorb up to 0.2%. When Polycarbonate is molded not well enough dried, problems with streaking or loss of physical problem will occur. To prevent these problems, the residual moisture levels in Polycarbonate pellets should not exceed 0.02% when they are processed.
Disclaimer
NOTICE:The information and data contained herein are given in good faith but do not constitute sales specifications.
NOTICE:The product properties may be changed without notice.
NOTICE: No freedom from infringement of any patent owned by SCPC or others is to be inferred. Because use conditions and applicable laws may differ from one location to another and may change with time, the Customer is responsible for determining whether products and the information in this document are appropriate for the Customer’s use and for ensuring that the Customer’s workplace and disposal practices are in compliance with applicable laws and other governmental enactments. SCPC assumes no obligation or liability for the information in this document. NO WARRANTIES ARE GIVEN; ALL IMPLIED WARRANTIES OF MARCHANTABILITY OR FITNESS FOR A PARTICULAR PURPOSE ARE EXPRESSLY EXCLUDED.
NOTICE: If products are described as “experimental” or “developmental”: (1) product specifications may not be fully determined; (2) analysis of hazardous caution in handling and use are required; (3) although SCPC may from time to time provide samples of such products, SCPC is not obligated to supply or otherwise commercialize such products for any use or application whatsoever.
To ask more questions on our products,please refer here
Contact Us
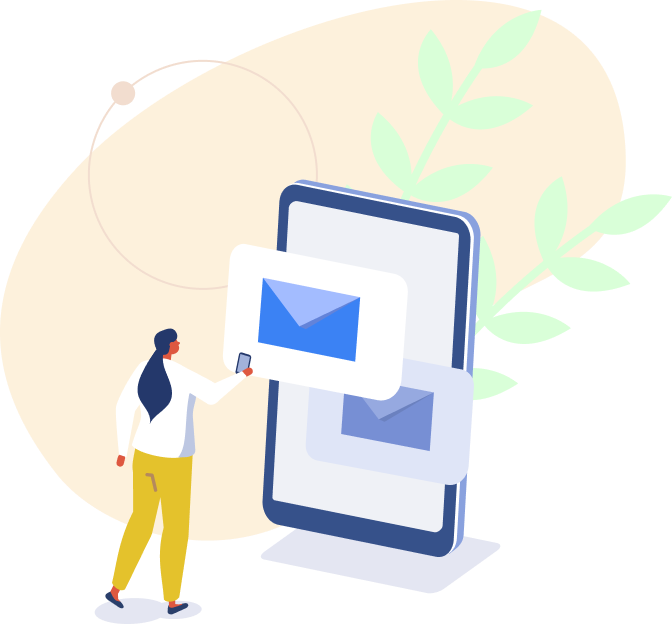
If you have any questions about our products or would like to know more about our products, please contact us using the form below.